IMPACT OF COVID-19 ON OUR ACTIVITIES IN 2020
Protecting the health and safety of our employees during the pandemic
Read moreHealth and safety performance
Our health and safety performance monitoring covers both PMI employees and contracted workers who are under the direct supervision of PMI but employed by a temporary employment agency (we had around 7,000 contracted employees per month in 2020). We also seek to continuously improve our monitoring of contractors when present on PMI premises.
In 2020, across our factories, offices, and fleet, our lost time incident rate (LTIR) for employees, contracted employees, and contractors was 0.08 (2019: 0.14). More specifically, it was 0.07 (2019: 0.12) for employees and contracted employees and 0.12 (2019: 0.23) for contractors. We do not set targets on lost time incidents, because we want to handle every single accident with the same level of importance, analysis quality, and mitigating actions regardless of whether the accidents involve or not lost time. We address equally all types of injuries happening to all people on our premises—employees, contracted employees, and contractors.
Our total recordable incidents rate (TRIR) was 0.12 (2019: 0.22)—which breaks down into 0.11 (2019: 0.20) for employees and contracted employees and 0.16 (2019: 0.32) for contractors.
Our LTIR and TRIR rates improved versus 2019, thanks to the strong commitment of our senior management, continued training and capacity-building, and heightened safety awareness across the organization.
We are proud of the progress made to date but remain cautious, as exceptional circumstances in 2020 driven by COVID-19 have positively impacted figures. We will keep strengthening our monitoring and remain committed to achieving a TRIR below 0.3 by 2025 in a sustainable manner.
In this chapter
- Impact of COVID-19
- Health and safety performance
- Working with contractors
- Safety in manufacturing
- Focus on fleet safety
- Employee well-being
- Building a smoke-free future starts with us
- Next steps
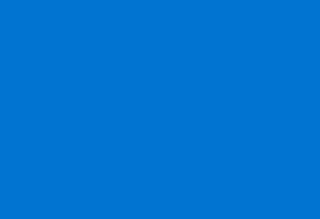
Health, safety, and well-being at work - topic overview
read moreWorking with contractors
Contractors are workers who are employed by or work on behalf of a third-party company contracted by PMI but who remain under the direct supervision of their employer. Typically, such workers are involved in project-specific or outsourcing arrangements.
The contractors with whom we work are employed by companies with varying approaches and requirements related to health and safety.
We had on average around 17,000 contractors per month in 2020 across our global organization. Their work typically includes specific projects (such as machine installation or construction), facility management (such as building maintenance), logistics (such as transportation and administration), or services such as canteens and medical centers available on PMI premises.
In 2020, our Health & Safety and Procurement teams reviewed our standards to further define health and safety requirements and performance measurement for contractors working on PMI premises. Moving forward, these more detailed measures will strengthen our reporting as we remain committed to achieving a TRIR of less than 0.30 for employees, contracted employees, and contractors by 2025 in a sustainable manner.
Although in previous years we had a zero-trend related to market fatalities, it is to our deep regret that we endured one market fatality in 2020 involving one of our contractors. The accident occurred during market field activities in Indonesia, involving challenging circumstances related to non-compliance with basic work at height safety standards. Detailed investigations have been carried out to understand root causes and identify ways to prevent such occurrences in the future. The lessons learned include process improvement in contractor management specific for raising the risk awareness regarding work at height and safe usage of ladders.
Safety in manufacturing
External certification helps us continuously improve and drive efficiency. In 2020, all our factories producing the equivalent of more than three billion cigarettes annually achieved certification to ISO 14001 and ISO 45001. The global multisite certification process included third-party audits of a sample of our sites, demonstrating that best practices are embedded across all our factories.
In our manufacturing facilities in 2020, our LTIR for employees and contracted employees was 0.07 (2019: 0.06). Our TRIR was 0.13 (2019: 0.17). Including contractors in the scope, our TRIR was 0.14, a decrease from 0.2 in 2019. No employee, contracted employee, or contractor fatalities occurred in our factories in 2020.
Following the deployment of behavioral observation systems (BOS) in 2019, we continued in 2020 to reinforce an “active caring” approach aimed at focusing employees’ attention on daily safety behaviors—their own and those of colleagues. Drawing on peer-to-peer observations, BOS allows for data-driven decision-making and helps us evaluate and improve our health and safety strategy. We continued engaging employees and delivering training on BOS to shop floor teams, supervisors, and high-level management across all our factories. Globally, we engaged over 90 percent of employees in our manufacturing sites in BOS in 2020, and they conducted an average of nine observations per employee every month, contributing directly to improvements in our TRIR.
Learning and data from BOS help us adjust our initiatives and inform our strategy. We plan to digitalize the system in 2021, which will allow us to better understand the causes of unsafe behaviors and better tailor our prevention programs.
Focus on fleet safety
Driving presents a risk to employees at PMI. We have around 23,000 cars on the road, covering around 370 million kilometers a year. The safety risks faced by our sales and distribution personnel, especially those at the wheel, are exacerbated in regions where road conditions can be hazardous. Road traffic accidents affect not only PMI staff but also the public, so fleet safety management is a top priority. During the year, we reinforced our fleet safety management system, strengthening our procedures and standardizing our incident reporting. We continued to engage fleet safety committee teams at each of our affiliates, composed of the head of local management and representatives of relevant business units.
The challenges we face in delivering safe working conditions relate to road conditions, law enforcement, and driving culture. Drivers almost always work alone, and we recognize that they may be under stress at times. Technology can help manage these risks, and we use telematics to monitor driver behavior to improve safety and efficiency. By the end of 2020, around 35 percent of our vehicles were equipped with telematics, and we plan to have all working tool cars equipped by the end of 2023.
In 2020, globally, we reduced collisions per million kilometers driven, achieving 0.53 (2019: 0.87), continuing the positive trend of the past seven years (2014: 1.8). We must consider COVID-19 impact in 2020 as a contributing factor, which additionally mitigated collision exposure risk, and we have improved our target, aiming to maintain our collision rate below <0.65 by 2022.
Although we continue to reduce collisions, it is to our deep regret that we endured road traffic fatalities in 2020, involving one PMI employee and five members of the public. The accidents occurred in two countries in Asia, involving challenging circumstances related to negligence of basic defensive-driving techniques, such as advance traffic anticipation and maintaining safe speeds for the road conditions or some elements of distracted driving. Robust investigations have been carried out to understand what happened and identify ways to prevent such occurrences in the future. The lessons learned include the necessity for a proactive risky driving detection platform, relying on a robust fleet safety management program and balance among behavioral programs, technology implementation, and a PMI fleet safety policy.
Employee well-being
Along with the many challenges, some positives have come from the need to adapt to COVID-19. One of these is the acceptance that remote work can be effective, productive, and, for some, a more satisfactory way of working compared with a full-time on-site presence. That said, sustained remote work presents its own challenges, and in-person interaction remains valuable. With this in mind, we have developed a global plan and adopted the concept of “Smart Work”—a hybrid of remote and office-based work—over the summer as the new standard way of working for PMI.
Our Smart Work philosophy enables employees to define more effective and efficient ways to achieve their objectives through greater flexibility in how and where they choose to work, facilitating increased productivity, flexibility, enjoyment, and ultimately balance in our everyday lives. A detailed suite of resources has been developed to guide markets in the implementation. The program is a post-COVID-19 initiative. Due to the COVID-19 resurgence in many countries during the second half of the year, to date we have launched Smart Work in three markets (India, Thailand, and Vietnam). In the markets not yet covered by Smart Work, our FlexAbility program allowing for remote work, a compressed workweek, part-time employment, and unpaid leave remain available, subject to local COVID-19 restrictions and guidance.
During the year, we launched a global Employee Assistance Program which provides employees and their families with psychological and emotional counseling support as well as legal and financial support. This program was initially launched in 52 countries where the service did not exist previously and, by the end of 2020, 75 countries were part of the global program, covering over 80 percent of our employees and their immediate family members. Initial feedback on the program was positive, with utilization in line with global norms for such a program.
During the early stages of the pandemic, communications from senior management emphasized understanding of and empathy for personal situations and the extra pressure that pandemic restrictions were putting on individuals and families. They set the expectation that people managers be flexible with work priorities, and employees prioritize care for themselves and their families. We hosted several panel discussions with senior leaders, employees, and outside experts and facilitated conversations on our internal social media channel to raise awareness of mental healthcare and destigmatize struggles, and asking for help. We also have an online learning platform with external expert resources for mental healthcare. We ran holistic resilience capability-building workshops for our top 200 leaders. Those workshops define resilience as dealing with everyday stress without compromising well-being, coping with setbacks, and adapting to change, and preparing proactively for future challenges.
As part of our regular employee listening, we ask employees once a year to answer the following question: How would you rate your current psychological or emotional well-being at present? This gets measured on a five-point scale from very bad to very good. In 2020, 58 percent of employees responded “good” or “very good.” We will track progress on this indicator and aim to achieve a 5 percent increase in 2021.
Building a smoke-free future starts with us: Leading by example
Across the organization, from our offices to our factories, we are doing our part to make our vision of a smoke-free future a reality. For any individual, and in turn an employee of our company, a smoke-free future means quitting cigarettes for good. The next best option for those who would otherwise continue to smoke is to switch completely to a smoke-free alternative such as an e-vapor or heated tobacco product. Our “Smoke-Free Employer” program brings this belief to life, with concrete action and information to educate and transform our workforce and workplaces. Being a large organization, it is imperative that we are as clear and as straightforward with our own teams on what the smoke-free future is, as we are with the rest of the world.
The basis of the program starts with reinforcing the message to employees that smoking is harmful and encouraging them to quit all nicotine and tobacco products altogether. The program also informs those who would otherwise continue to smoke that better alternatives to cigarettes are available. Coupled with education and awareness building, we have created sessions on both understanding those alternatives, as well as the science behind them, for employees to make more informed choices. The final piece of the Smoke-Free Employer Program is taking all available actions to ban indoor smoking of cigarettes, remove indoor cigarette smoking rooms, and for employers to offer the use of smoke-free alternatives in accordance with local laws and regulations.
PMI affiliates around the world have been implementing this program. Once locations have successfully implemented the Smoke-Free Employer Program, they can apply to become “Smoke-Free Culture” certified by an independent third-party body. The protocol for the “Smoke-Free Culture” certification was developed by TÜV AUSTRIA. It is available to organizations including events, corporations, and public authorities (e.g., municipalities) recognizing their commitment to reducing smoking and cigarette consumption through tangible actions and measurable objectives. “Smoke-Free Culture” certified organizations plan, support, implement, monitor, and continuously improve a set of actions with the aim to ensure this vision.
PMI’s Greek affiliate Papastratos was the first affiliate to implement the Smoke-Free Employer Program and to become “Smoke-Free Culture” certified in 2018. To date, in addition to Greece, PMI affiliate offices in Canada, Japan, Lithuania, the Czech Republic, the Slovak Republic, and the U.K. have been “Smoke-Free Culture” certified. Additional affiliates are currently in preparation for the certification process, and our goal is for PMI to become the first globally “Smoke-Free Culture” certified company.
Performance highlights
-
0.12
Total recordable incident rate (iTRIR) per 200,000 hours worked for PMI employees, contracted employees, and contractors
-
100%
of our manufacturing facilities certified OHSAS 18001 and ISO 14001
Next steps
At the end of 2020, many countries were facing a second wave of COVID-19, with governments issuing new requirements to try to slow the spread of the virus. To contribute to mitigation efforts, we remain committed to promoting the behaviors and measures recommended by authorities and public health experts. We will stay diligent and ready to react as the situation evolves.
In our manufacturing facilities and fleet, we will continue to deliver initiatives to improve safety and meet country-level and global targets.
Specific priorities for 2021 are to establish an integrated data-driven roadmap of priority action to support the holistic well-being of employees across the company. This will include accelerated promotion of mental health support worldwide. We will continue to actively encourage talking about mental health and sharing stories to reduce stigma, as well as providing training to employees and line managers to understand the impact of mental health issues, recognize signs of struggle, and know how to support themselves and their teams.
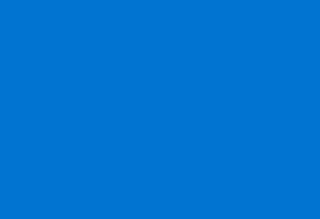
Performance metrics
View dataThis online content about our Integrated Report should be read in conjunction with PMI’s 2020 Integrated Report. The information and data presented here cover the 2020 calendar year or reflect status at December 31, 2020, worldwide, unless otherwise indicated. Where not specified, data come from PMI estimates. Please also refer to 'About this report' on page 3 of the 2020 Integrated Report for more information. Aspirational targets and goals do not constitute financial projections, and achievement of future results is subject to risks, uncertainties and inaccurate assumptions, as outlined in our forward-looking and cautionary statements on page 145. In the 2020 Integrated Report and in related communications, the terms “materiality,” “material,” and similar terms, when used in the context of economic, environmental, and social topics, are defined in the referenced sustainability standards and are not meant to correspond to the concept of materiality under the U.S. securities laws and/or disclosures required by the U.S. Securities and Exchange Commission.