Our approach
Our operations rely on securing high-quality, cost-effective, and fit-for-use materials and services from suppliers, which are expected to adhere to PMI’s sustainability-related requirements. These requirements form the basis for collaboration with PMI and are set out in our Responsible Sourcing Principles (RSP)—first introduced in 2017 and revamped in 2023. To achieve tangible environmental and social improvements, we seek to identify and address actual and potential risks while seizing opportunities to create a positive impact in the communities in which we and our suppliers operate.Our approach to sustainable supply chain management is based on:
- Leveraging the reach and understanding of our supply base to proactively engage our suppliers to implement impactful programs, such as tackling climate change, preserving nature, and improving the quality of life of people in our supply chain
- Assessing risk linked to the nature of materials or services we purchase and the location they are sourced from
- Conducting supplier due diligence and assessing their sustainability performance and reporting capabilities
- Driving continuous improvement towards compliance with sustainability requirements through supplier capability building
- Embedding sustainability criteria in strategic sourcing decisions and supplier selection process
As part of our procurement practices, we identify and screen suppliers for business relevance and potential environmental, social, and governance-related risks before engaging with them.
Our screening methodology includes country-specific, sector-specific, and commodity-specific risks to determine a list of significant suppliers through a sustainability lens. In 2024, we engaged with approximately 1,000 significant suppliers. Significant suppliers are those identified as having a substantial risk of negative sustainability-related impact, significant relevance to the business, or a combination of both.
However, not all significant suppliers are critical to our business. Critical suppliers are linked to the nature of materials or services they provide to the business (e.g., pulp and paper and electronic components). In 2024, we had 209 critical suppliers. Significant and critical suppliers go through a rigorous assessment process.
Our supply chain sustainability due diligence is guided by our RSP, which aligns with the UN Guiding Principles on Business and Human Rights (UNGPs), the 10 principles of the UN Global Compact, and the International Labour Organization (ILO) Conventions. It also helps us build preparedness for anticipated and pending legislation such as the EU Corporate Sustainability Due Diligence Directive (CSDDD) and EU Deforestation Regulation, among others.
The RSP details our expectations and sets process and performance requirements for our suppliers. We expect all our suppliers to adhere to the mandatory section of our RSP requirements and address identified gaps to continuously improve their sustainability performance.
To monitor RSP adherence, we apply tailored due diligence mechanisms within specific segments of our supply chain. In our tobacco supply chain, our work is governed by our Good Agricultural Practices (GAP) and Agricultural Labor Practices (ALP) Code, which are operationalized at the farm level by field technicians working year-round with the farmers contracted by PMI and our suppliers. In our electronics supply chain, we leverage the work of the Responsible Business Alliance (RBA) and its adjacent programs. For monitoring of direct materials, indirect materials and services, and third-party leaf suppliers, we collaborate through our preferred partner, EcoVadis.
Adherence to our RSP—and to GAP for our tobacco supply chain—is being built into our contractual agreements with suppliers. We use a suite of tools, including self-assessment questionnaires, third-party assessments, on-site audits, and field visits to monitor performance.
The RSP has been published in 27 languages to facilitate supplier understanding and its deployment. As originally planned with the revamp of the RSP, all contractual commitments will include an adherence requirement by 2025.
PMI employees who have regular interaction with suppliers have been requested to complete RSP training. Internal capability building on RSP has been split into sections specifically dedicated to RSP: Fundamentals and Advanced, as well as other non-related sessions that explain RSP.
Management
The sustainable sourcing of goods and services involves broad cross-functional collaboration within PMI. Operational responsibility for PMI’s supply chain is executed by our Global Technical Operations and Operations Services teams. It is overseen by our Senior Vice President, Operations.Fostering collaboration with our suppliers
We continue to strengthen our engagement beyond Tier 1 suppliers partnering with companies that have diverse strategies, priorities, and cultures—to jointly progress on our sustainability journey. Our engagement is based on common values and shared aspirations to achieve sustainability goals.In 2024, we held several face-to-face events that facilitated
cross-industry collaborations. To maximize our outreach, we
held numerous webinars, building capability and supporting
our suppliers. Procurement takes every opportunity when
interacting with suppliers to engage in meaningful
conversations on sustainability.
During the year, we also continued and expanded our Sustainability Accelerator program, which aims to leverage our learnings, and best practices to build supplier capability. The Accelerator’s integrated approach is developed to expedite the sustainability progress of our suppliers in relation to their performance and reporting in order to comply with a fast-moving regulatory landscape.
A team of PMI experts collaborates with each supplier team individually to build capabilities and share PMI’s sustainability progress, learnings, and methodologies. By investing in our suppliers’ learning, we not only enhance our supply chain’s resilience but also ensure sustainability performance and reporting on impacts for both our own operations and our broader supply chain in the context of evolving regulatory requirements.
All insights and learnings gained through the program are then used to further enhance and optimize the offering for our diverse value chain. Following a successful pilot with five suppliers across our broader supply chain in 2023, the program expanded to include 18 additional suppliers in 2024, selected based on relevance for PMI and maturity.
Initially, the program focused on climate change and sustainability fundamentals, such as strategy development and deployment systems. We plan to expand the program in 2025 to reach more suppliers while broadening the scope to include nature-related topics such as biodiversity, forests, and water. Additionally, in the medium term, we expect to expand to social and human rights-related matters, with a roll out on these topics planned for 2026.
PMI's Sustainability Accelerator
In 2023, PMI initiated the Sustainability Accelerator program to leverage our learnings and accelerate the sustainability journey of our suppliers. Fostering an integrated approach, the program covers sustainability-related matters from a performance and reporting standpoint. Five companies of different industry sectors, geographies, and sizes were enrolled in the initial pilot.
The primary focus of this program is to accelerate the delivery of sustainability programs agreed to between PMI and suppliers. The learnings and insights can be used to improve the program and optimize it for our diverse value chain.
The pilot was focused on climate change and sustainability fundamentals (covering, for example, strategy development and deployment systems). A team of experts collaborated with each supplier team individually to build capability and share PMI’s progress, learnings, and methodologies to help accelerate our supplier’s progress.
Overview of our supply chain in 2024
With over 21,400 tier 1 suppliers globally, our supply chain spend amounted to approximately USD 14 billion in 2024. Our global supply chain is organized into two main streams: direct spend (focused on materials used to manufacture our finished products) and indirect spend (focused on goods and services necessary to operate our business).Currently, our global supply chain supports our two main finished product categories: smoke-free products that are increasing in resource allocation in line with our growth strategy, and cigarettes.
The majority of our supply chain spend for smoke-free
products derives from our direct spend on electronics. During
2024, as we purchased more tobacco than in past years to
replenish inventory, the overall proportion of supply chain
spend attributable to electronics dropped relative to our
overall spend on tobacco, which serves both our cigarettes
and smoke-free products. As a result, smoke-free product
supply chain spend decreased slightly to 40 percent (2023:
41 percent).
The supply chain categories exposed to the highest sustainability risks identified to date pertain to our direct spend and include:
- Agricultural supply chain
- Tobacco production, with the main risks associated with working conditions, child labor, climate change, access to water, and the socioeconomic well-being of farming communities.
- Paper and pulp-based materials, with the main risks linked to biodiversity, climate change and water management.
- Electronics supply chain
- Electronics manufacturing, with the main risks relating to potential social issues on ethical recruitment, working conditions of migrant workers, and working time.
A glance at our path to integrate the data from Swedish Match
Supply chain data and information in this section does not include Swedish Match. Though not drastically different, we are working to integrate our respective supply chains, seeking to leverage their efficiencies while remaining mindful of new elements linked to the oral smokeless category. Such integration requires us to harmonize the procedures, systems, and performance indicators we have in place. As we do so, we also expect to find synergies and harness the expertise and best practices of each company. Our integration efforts will include particular attention on the nicotine production supply chain for oral products, addressing the distinct sustainability challenges it poses. We provide further details on our efforts in the Improve the quality of life of people in our supply chain, Tackle climate change, and Preserve nature sections of this report.Sustainability performance in our supply chain
Proactively managing the sustainability performance of our suppliers is paramount to our ability to identify, prevent, and mitigate sustainability-related risks. By doing so, we ensure PMI’s readiness to comply with existing and upcoming regulations. By endorsing robust governance, we seek to secure our success in achieving our environmental aspirations and improving the livelihoods of people in our supply chain.Our supply chains are long and complex. Our procurement teams have a robust engagement plan with significant suppliers to drive impact.
Depending on the type of risk and in line with our supplier segmentation, we request suppliers to disclose their sustainability-related performance through EcoVadis or RBA. Disclosures can be made via desk-based assessments or on-site audits. They are followed by a review touchpoint performed by our sustainability procurement team, which may indicate a need for a corrective action plan. Procurement teams address supplier performance through annual meetings, quarterly performance reviews, or more frequently if needed depending on assessment outcome and the criticality of issues identified.
While our procurement teams monitor supplier improvement, it is the suppliers’ responsibility to put in place a corrective action plan (CAP) and drive improvements in their supply chain. These CAPs are reviewed and additional support to suppliers is offered through internal experts or dedicated external tools.
We aspire to 100 percent of spend with critical suppliers from whom PMI sources be done sustainably by 2025. In 2024, we made continued progress, reaching 94 percent (2023: 91 percent).
1
For definition of critical and significant suppliers, see the Glossary.
2
Sustainable sourcing is determined based on a minimum threshold score of 45 out of 100 in EcoVadis (direct materials) or 125 out of 200 in RBA with no open priority issues (electronics). All traceable tobacco purchased from monitored farmers is considered
sustainable.
Direct materials supply chain
To assess direct materials suppliers holistic sustainability performance across environment and social, ethics, and responsible purchasing domains, we use EcoVadis. It is largely aligned with PMI’s RSP and gives us an opportunity to enhance our accountability while also providing actionable insights on potential improvement areas.During 2024, 135 suppliers representing 92 percent of our total direct material spend were assessed. Of these, 92 percent were determined to be sourced sustainably by PMI, based on the score provided by the assessment platform. Only 8 percent were below the minimum threshold required. Suppliers with a low score were mandated to develop and implement a CAP, and report progress.
CAPs are segmented by theme, indicator (policy, action or reporting), and priority level. Depending on priority, suppliers of direct materials are requested to close identified gaps in an agreed timeframe, and to conduct a reassessment. Our procurement team engages directly with suppliers to provide necessary support and capability building. We actively support suppliers’ CAP reviews to drive performance improvement. For direct materials alone, 6 suppliers (representing approximately 0.3 percent of our critical direct materials suppliers) were reassessed in 2024 (2023: 13 suppliers representing 10 percent). On average, the EcoVadis score of suppliers that underwent reassessment increased by 18 points, which signals a strong commitment and investment made by our suppliers.
Electronics supply chain
As our Company transforms, we are increasingly focused on the sustainability of our expanding electronics manufacturing supply base. This supply chain is complex and dynamic, and carries inherent risks
and challenges, including the potential presence of conflict minerals.
We also continued to participate in RBA’s Validated Assessment Program (VAP)—the standard for on-site compliance verification and effective, shareable audits. Under this program, independent external auditors review our electronics suppliers’ sustainability performance against the RBA Code of Conduct, which is aligned with PMI’s RSP requirements. To gather additional audit data, we leverage customer managed audits (CMAs), a comparable audit standard recognized by RBA.
In 2024, 100 percent of our spend with critical electronics suppliers covered by VAP or CMA audits and the average RBA score of our suppliers was 174 (out of a maximum of 200), compared with an RBA average for our suppliers of 170 in 2023. Audit reports revealed several common issues across suppliers on social issues, including working hours, emergency preparedness, and wages and benefits.
To drive improvement in these areas, we continued to leverage two key RBA programs: the Responsible Factory Initiative (RFI), which provided support to supplier factories to implement the RBA code, and the Responsible Labor Initiative (RLI), which equipped suppliers with tools to address potential forced labor issues associated with migrant workers.
We successfully completed the pilot of the RFI in two factories in China, and the RLI with eight recruitment agencies in Nepal in 2024. We continued rolling out the RFI program to an additional 10 factories in 2024, with a plan to further expand the program in 2025.
Conflict minerals
We are committed to operating with integrity and to responsibly source 3TGs (tin, tantalum, tungsten, and gold), which are potentially used in our products.
Our 2024 conflict minerals submission to the U.S. Securities
and Exchange Commission (SEC) covering the year ended
December 31, 2023 showed that approximately 92 percent of
the smelters or refiners (SORs) in our conflict mineral supply
chain are engaged with Responsible Minerals Assurance
Process (RMAP) or RMAP-Active. The remaining
approximately 8 percent were contacted and requested to
conduct due diligence to verify whether they sourced 3TGs
from the Covered Countries (as defined by the U.S. SEC)
during 2023.
In 2024, we updated our Responsible Sourcing of Minerals Policy for better alignment with our RSPs and the OECD Due Diligence Guidance. Our Policy effectively articulates PMI’s existing due diligence efforts, including requirements for suppliers, and demonstrates a stronger commitment to minerals supply chain due diligence. It provides details on our approach to consequence management and also establishes a foundation for PMI to expand due diligence to other minerals and geographies beyond those in scope of the U.S. SEC Ruling.
Following a pilot in 2023 where we increased the frequency of
the conflict minerals data collection to twice a year, in 2024
we rolled it out to all PMI suppliers. This increased monitoring
improved the quality of the data collected.
Cobalt, which is used in the batteries that power our smoke-free devices, is also linked to unethical mining practices. While the quantities required for our products are minor relative to the global market size, we are leveraging the RMI approach for due diligence in our cobalt supply chain to identify and address potential human rights risks.
In 2024, all our battery suppliers responded to a PMI request. Subsequent due diligence indicated that, as of December 31, 2024, each of the 40 smelters from which PMI battery suppliers source cobalt were on RMI’s conformant list. We continue to engage with our suppliers to improve visibility into this complex supply chain and enhance our due diligence framework.
Maintaining full traceability and monitoring in our tobacco supply chain
To a large extent, responsible sourcing stems from strong relationships on the ground. PMI’s Integrated Production System (IPS) connects leaf suppliers and farmers beyond the customary boundaries of a commercial relationship and enables direct technical support, agronomic advice, financial loans, and various other services. Our IPS covers 96 percent of our tobacco purchases in 2024, the excluded amount, originated from India.The IPS is vital to providing traceability and visibility in our supply base; it enables the deployment of our GAP and ALP monitoring and remediation system down to the farm level. At the center of this system are field technicians, employed by PMI or our third-party suppliers. These technicians visit each farm on average five times during the crop season and monitor the implementation of our GAP and ALP codes. They also provide agronomic assistance, deliver training to farmers (e.g., on our GAP and ALP codes), identify and address labor issues, and monitor the implementation of improvement plans.
In 2024, field technicians enabled us to monitor compliance with GAP by all farmers supplying tobacco to PMI under the IPS.
Due to varying local realities, partnering with third parties that can provide tailored support and respond to local needs is crucial. Where possible, we partner with local NGOs that can support and monitor GAP and ALP implementation
Overview of tobacco sourcing under PMI’ Sustainable Tobacco Supply Chain (STSC)
Because of our transition toward smoke-free products, we are observing a steady decline in our overall tobacco demand (approximately 16 percent decrease since 2016). However, over the past two years, our tobacco sourcing has seen a slight increase. This is primarily due to the necessity of replenishing inventory stock and responding to the resilience of the combustible product category.
Despite this recent limited uptick, the overall trajectory
points toward a continued decline, with smoke-free
products requiring on average significantly less tobacco than
traditional combustible cigarettes. The volume of tobacco
we purchased in 2024 amounted to 309,000 tons (2023:
308,000 tons). During the year, we sourced tobacco grown
across 21 countries, with most of our volume coming from
India, Brazil, Indonesia, Italy, Argentina, Malawi, China, the
U.S., Turkey, and Tanzania
Indirect materials and services supply chain
In 2024, we expanded our supplier due diligence efforts to significantly increase our engagement with indirect materials and services (IM&S) suppliers.IM&S spend is complex and involves a large number of small suppliers that serve the specific needs of different markets. It requires a significant effort to engage these suppliers and ensure they perform due diligence on their supply chains.
Over 500 of our IM&S suppliers (representing 61 percent of our IM&S supplier base) have been engaged in the due diligence program through EcoVadis assessments. Central, regional and local procurement teams actively reach out to suppliers to increase engagement. Prior to supplier outreach, internal onboarding sessions are conducted for the procurement community.
Over 58 percent of PMI IM&S suppliers disclosed their environmental and social efforts through EcoVadis in 2024, of which over 82.5 percent reached PMI’s minimum performance requirements
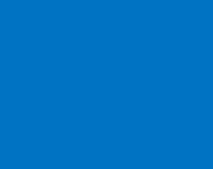
View all Fundamentals
Read moreThis online content about our Integrated Report should be read in conjunction with PMI’s Integrated Report 2024. This report includes metrics that are subject to uncertainties due to inherent limitations in the nature and methods for data collection and measurement. The precision of different collection and measurement techniques may also vary. This report includes data or information obtained from external sources or third parties. Unless otherwise indicated, the data contained herein cover our operations worldwide for the full calendar year 2024 or reflect the status as of December 31, 2024. Where not specified, data comes from PMI financials, nonfinancials, or estimates.
Unless explicitly stated, the data, information, and aspirations in this report do not incorporate PMI’s wellness and healthcare business, Aspeya. Regarding the Swedish Match acquisition, completed late 2022, unless otherwise indicated, this report includes information pertaining to its sustainability performance. Please also refer to "This report at a glance" on page 2 of the PMI’s Integrated Report 2024 for more information. Aspirational targets and goals do not constitute financial projections, and achievement of future results is subject to risks, uncertainties and inaccurate assumptions, as outlined in our forward-looking and cautionary statements on page 206. In PMI’s Integrated Report 2024 and in related communications, the terms “materiality,” “material,” and similar terms are defined in the referenced sustainability standards and are not meant to correspond to the concept of materiality under the U.S. securities laws and/or disclosures required by the U.S. Securities and Exchange Commission.